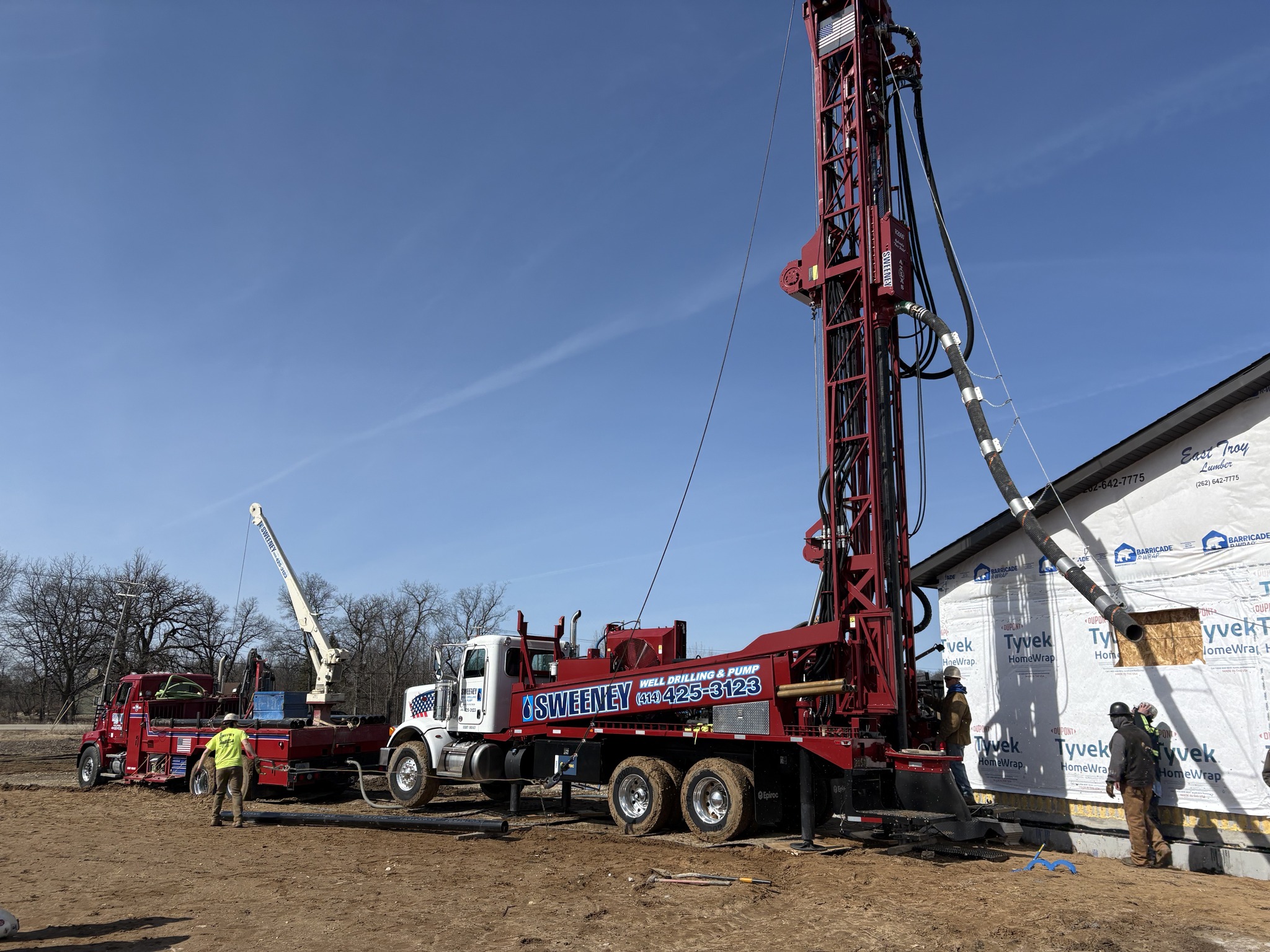
Professional water well drilling relies on powerful equipment and expert techniques. In the United States, millions of people depend on private water wells for drinking water. Drilling a water well is not a DIY task – it requires specialized rigs, trained crews, and adherence to regulations to ensure a safe, clean water supply. Professionals follow a series of well-defined steps, use appropriate drilling methods for the local geology, and implement safety and environmental safeguards throughout the process. Below, we break down how the pros get it done, from planning to pumping.
Step-by-Step Professional Well Drilling Process
- Site Selection & Planning: The first step is choosing an optimal location for the well. Drillers consider accessibility for heavy equipment and a spot safely distant from potential contamination sources like septic systems, livestock yards, or fuel tanks. They also evaluate geology and past well records in the area to estimate how deep they must drill to reach a reliable aquifer. Proper siting ensures the well will provide clean water (for example, placing it so that rain runoff flows away from the well, not toward it).
- Permits and Paperwork: Before any drilling begins, professionals secure the necessary permits from state or local authorities. In most states, a well cannot be drilled without prior approval, and the work must be done by a licensed well driller. The permitting process usually involves submitting plans or a Notice of Intent to drill, paying fees, and meeting any site-specific requirements (for instance, minimum distances from sewer lines or required casing depth). Many areas also require that a well log or completion report be filed after drilling, and some may schedule an inspection during key steps, such as when sealing the well.
- Mobilization & Rig Setup: Once permitted, the drilling contractor moves the drilling rig and support trucks onto the site. The crew prepares the area by clearing and leveling the ground if needed, ensuring there is enough room to operate the rig safely. Heavy rotary drilling rigs (often truck-mounted) are commonly used. The rig is positioned over the chosen spot, and the mast (derrick) is raised. Before actual drilling, professionals also take safety precautions during setup – for example, marking or avoiding underground utilities by contacting the local “Call 811” service to locate pipes and cables in the vicinity. This prevents accidental hits to gas, electric, or water lines when drilling starts.
- Drilling the Borehole: With the rig in place, the crew begins drilling the well borehole using a method suited to the ground conditions. In softer soils (like clay or sand), a rotary drill with a rotating bit is used, often with drilling mud (fluid) pumped down to carry cuttings out of the hole. In harder rock formations, an air rotary system with a pneumatic down-the-hole hammer may be employed – compressed air forces rock chips up from the hole as a hammer bit pulverizes the rock. In some cases, traditional cable tool (percussion) drilling may be used, where a heavy bit repeatedly lifts and drops to break the rock, although this method is slower. Modern rigs can drill wells hundreds of feet deep, as needed, to reach aquifers. Throughout drilling, the crew monitors drilling parameters and watches for signs of water in the formation. The borehole diameter is typically a few inches wider than the final well casing.
- Casing Installation: After reaching the desired depth and sufficient water yield, the next step is installing the well casing. The casing is usually a steel or heavy-duty PVC pipe that lines the borehole. Its purpose is to keep the hole open and prevent the sides from collapsing, as well as to block contaminants from shallow layers. The crew lowers lengths of casing into the hole, joining them together (by welding steel casing or threading PVC) until the casing extends from the bottom of the well up to the surface. A section of the casing near the bottom may have a well screen (slots or perforations) to allow water from the aquifer to enter while keeping out sand and sediment. At the surface, the casing will protrude above ground and later be fitted with a sanitary well cap to keep bugs and debris out.
- Grouting (Sealing the Annulus): Once the casing is set, professionals seal the gap between the outside of the casing and the borehole wall – known as the annulus – by pumping in a sealing material (usually a cement-based grout or bentonite clay slurry) from the bottom of the annulus upward to the surface. This creates an impermeable seal that prevents surface water or shallow contaminated groundwater from seeping down along the outside of the casing and contaminating the well. Grouting is a critical step for groundwater protection and is often legally required to meet state well construction standards. In many jurisdictions, an inspector may need to witness this procedure to confirm it’s done correctly. After grouting, the seal is allowed to set (harden).
- Well Development & Cleaning: With the well bore drilled, cased, and sealed, the driller “develops” the well to improve its performance. Well development involves cleaning out fine sediments and drilling mud from the well and encouraging water flow from the aquifer into the well. This can be done by methods such as air surging, backwashing, or pumping the well at a high rate to flush out particles. Development is vital for clearing cloudy water and optimizing the well’s yield. The crew will typically continue development until the water runs clear and the well is producing at a stable rate.
- Pump Installation & Testing: After the well itself is constructed and developed, the final step is to install the pumping equipment. A submersible pump (for deep wells) or jet pump (for some shallow wells) is lowered into the well casing, with power cables and a water delivery pipe connected. The top of the well is sealed with a well cap or pitless adapter to prevent contamination. The system is then connected to a pressure tank and plumbing as needed for the end user. Once everything is in place, the new well is test-pumped, and the water is sampled. Professionals often test the water for basic quality parameters and may disinfect the well with chlorine to ensure any bacteria introduced during drilling are eliminated. In many states, a water sample must be submitted to a lab or the local health department to certify that the well meets safe drinking water standards. Only after these steps is the well ready to provide a reliable supply of clean water.
Types of Drilling Equipment and Methods
Professional well drillers use different types of rigs and drilling techniques depending on the project needs and local geology. Modern drilling rigs are usually large, truck-mounted machines. The choice of drilling method can affect how efficiently a well is drilled in various soil or rock conditions. Below are the main types of drilling equipment used in water well construction:
- Rotary Drilling Rigs: The most common equipment for water wells, rotary rigs use a rotating drill bit to grind through soil and rock. A heavy drill bit (often a tri-cone roller bit or PDC bit) is attached to drill pipes and rotated by the rig’s engine or hydraulic system. As it cuts the formation, a circulating fluid (water or drilling mud) is pumped down the drill pipe; it carries the crushed rock (cuttings) back up to the surface. Rotary drilling is fast and efficient in many ground conditions, and the drilling fluid helps to cool the bit, lift cuttings, and keep the borehole stable. Most residential and commercial water wells today are drilled with rotary rigs.
- Air Rotary (Pneumatic) Rigs: Air rotary drilling is a variation of rotary drilling that uses compressed air instead of liquid drilling mud to clear cuttings. Often paired with a down-the-hole air hammer, this method is excellent for hard rock formations. The air hammer is a pneumatically driven percussive bit that rapidly strikes the rock while the drill string rotates, essentially combining rotary and hammering action. Air rotary rigs blow the crushed rock chips up and out of the borehole with air circulation. This method is commonly used in regions with consolidated rock and is known for its speed in penetrating hard strata. It also keeps the borehole dry, which can be helpful when trying to identify water-producing zones.
- Cable Tool (Percussion) Rigs: An older but still-practiced method, cable tool drilling (also called percussion drilling) involves repeatedly dropping a heavy chisel-like bit into the borehole to break up earth and rock. The fragments are periodically bailed out of the hole. Cable tool rigs do not use continuous rotary motion; instead, the drill string is lifted and dropped in a pounding action. This method is slower than rotary drilling but has the advantage of simplicity and low cost in certain situations. Cable tool rigs were common in the early days of well drilling and are capable of drilling in formations where rotary drills might have trouble. Today, most professional drillers reserve cable tool methods for specialized circumstances, since rotary and air rotary rigs have higher productivity.
Other drilling methods and equipment can include auger drilling (using a large helical auger in very soft or shallow formations) and sonic drilling (using high-frequency vibration), but these are less common for water wells. A professional driller will choose the rig type and method best suited to the geological conditions and the well specifications.
Regulations, Permits, and Inspections
Professional well drilling in the U.S. is tightly regulated to protect public health and groundwater resources. Rules can vary by state (and even county), but here are some key legal considerations:
- Licensing: Almost all states require that water wells be drilled by a licensed well contractor. Licensing ensures the driller has the necessary training, experience, and knowledge of regulations. Homeowners in some states might be allowed to dig or drill their own well on their property, but they still must adhere to permit rules and construction standards. Doing it without professional help is generally discouraged due to the complexity.
- Permitting: Before drilling, a permit or filing is usually required. This means the driller (or well owner) must apply to the appropriate agency (often a state environmental agency or local health department) with details about the proposed well. The permit process ensures wells are placed properly (respecting setbacks from septic systems, property lines, etc.) and that the planned construction meets minimum standards. It’s illegal in many areas to drill a well without first obtaining the necessary authorization.
- Well Construction Standards: State and local regulations set standards for how a well must be built. These standards cover things like the minimum casing diameter and thickness, how deep the casing must go, the requirement to grout the annular space, and installing sanitary caps. Such rules are designed to prevent groundwater contamination and ensure a long-lasting, safe well. Drillers follow these codes closely, and deviations are not allowed without approval.
- Inspections and Reporting: Depending on the jurisdiction, there may be inspections at one or more stages of the well drilling process. A common point of inspection is during the grouting of the well, because a proper seal is critical for protecting the aquifer. After the well is completed, the driller usually must submit a well completion report or log to the state, detailing the depth, geology encountered, water levels, and construction details. In some states or counties, the new well’s water must pass a bacteria test or other water quality tests before it’s approved for use. Failing to comply with reporting or inspection requirements can result in fines or orders to modify the well.
Tip: Always hire a contractor who is familiar with your state’s well regulations. They should handle the permitting process for you and ensure the well meets all legal requirements. This not only keeps you in compliance with the law, but also ensures your well is constructed to a safe standard.
On-Site Safety Practices
Drilling a well is a construction project that comes with various hazards, so professional crews make safety a top priority. Here are some of the safety best practices and precautions followed on well drilling job sites:
- Worker Training and Certification: Crew members are trained in the operation of drilling equipment and safety protocols before going out to a job. They conduct safety meetings or Job Safety Analyses (JSAs) to identify site-specific hazards each day. Experienced drillers know how to handle equipment safely and how to respond to issues like tools getting stuck or encountering unexpected gas pockets. Many follow OSHA guidelines for drilling operations, and companies often have internal safety programs to ensure every worker knows their role and the risks involved.
- Protective Gear (PPE): On a drill site, all personnel wear appropriate personal protective equipment. This typically includes hard hats, steel-toe boots, safety glasses, and gloves. Loose clothing or jewelry is avoided because it can get caught in rotating machinery. Depending on conditions, hearing protection (for loud engine noise), dust masks or respirators (for dusty conditions), and high-visibility vests may also be used. Sun protection is important for crews working long hours in the sun.
- Equipment Safety and Maintenance: The drilling rig and associated equipment (like compressors, generators, hoists) are regularly inspected and maintained to prevent malfunctions. Hydraulic lines, cables, and bits are checked to ensure they are in good condition before work starts. Safety guards and emergency shut-offs on the rig are kept functional. Only authorized, trained crew operate the machinery, and others keep a safe distance during active drilling. If any unusual vibration, noise, or condition occurs, the crew pauses operations to address it rather than risk a breakdown or accident.
- Site Hazard Controls: The work area around the rig is kept organized to avoid trips and falls; hoses and tools are stowed properly. The drilling site may be cordoned off to keep bystanders at a safe distance. One critical safety measure is locating underground utilities prior to drilling—professionals contact the “One Call” system (811) to have utilities marked, preventing dangerous hits to gas or electric lines. The crew remains alert for overhead power lines as well. Additionally, heavy components like drill pipes are lifted with proper equipment (hoists, hydraulic winches) to avoid manual lifting injuries. Clear communication (often via hand signals or radios) is used so everyone knows when equipment is operating or when it’s safe to approach.
- Emergency Preparedness: Professional drillers prepare for the unexpected. They keep first aid kits on site and often have someone trained in first aid. Fire extinguishers are mounted on rigs in case of engine or fuel fires. If the drilling is deep and there’s any risk of encountering natural gas, the crew has gas monitors and ventilation ready. In remote areas, the team has a communication plan (like cell or satellite phone access) to call for help if needed. By anticipating potential problems—whether it’s a sudden storm, equipment failure, or an injury—the crew can respond quickly. Safety protocols minimize risk and help ensure everyone goes home healthy.
Environmental and Groundwater Protection
Protecting the environment—especially groundwater quality—is a fundamental concern during well drilling. A professionally drilled well is designed not just to tap a water supply, but also to safeguard the aquifers and surrounding ecosystem. Here’s how drillers minimize environmental impact and protect groundwater:
- Aquifer Protection via Casing & Grout: Installing the well casing and grouting the annular space are key defenses against contamination. The casing and grout prevent surface runoff or near-surface pollutants from seeping down the outside of the well into clean groundwater. They also prevent the well from interconnecting different water-bearing layers.
- Maintaining Safe Distances (Setbacks): Environmental regulations require wells to be drilled a safe distance away from potential contamination sources. For instance, there are minimum setback distances from septic drain fields, manure storage, fuel tanks, or industrial sites. By respecting these setbacks (often 50 to 100 feet or more, depending on local law), drillers ensure the well is not directly down-gradient of pollution sources. These precautions protect the long-term quality of the groundwater drawn by the well.
- Proper Disposal of Drilling Byproducts: The drilling process creates spoil in the form of rock cuttings, drilling mud, and water with sediment. Professional drilling companies manage these byproducts responsibly. Excavated mud and cuttings are often captured in a pit or container at the site; afterward, they may be backfilled on-site once dried or disposed of properly according to regulations. Fuel and oil for the rig are handled carefully—drip pans may be used under machinery, and any spills are cleaned up immediately with absorbent materials to prevent soil contamination.
- Minimizing Land Disturbance: Well drilling typically has a smaller footprint than large construction projects, but care is still taken to minimize disturbance to the land. Crews use existing access paths or stable ground to avoid damaging vegetation. If they had to dig a pit for mud circulation, they fill and restore it. After the well is completed, any debris is removed, and erosion control measures (like silt fencing or straw wattles) may be put in place if the soil was disturbed, especially on slopes, to prevent sediment runoff until vegetation re-establishes.
- Abandoning Unused or Old Wells: Environmental protection during drilling isn’t just about the new well—it also involves properly closing any old or test wells on the property. If a new well replaces an existing one, the old well must be properly abandoned by filling it with grout or clay to seal it top to bottom. Simply leaving an old well open or unused can allow contaminants or animals to fall straight into the groundwater. Proper abandonment prevents an unused well from becoming a direct conduit for pollution.
Conclusion: Trust the Professionals
Drilling a water well is a complex task that marries geology, engineering, and environmental science. From securing permits and bringing in the right rig, to skillfully drilling and casing the borehole, and then ensuring everything is safe and up to code—it’s clear why professional expertise is indispensable. A properly drilled well can provide decades of clean water, but a poorly executed one can lead to contamination, equipment failure, or legal headaches. When you need a new well, the best step you can take is to hire a licensed, experienced well driller.
Call to Action: If you’re considering a water well for your property or need service on an existing well, don’t go it alone. Reach out to a qualified professional who knows the local regulations and ground conditions. Use the convenient driller lookup tool on DrillerDB to find licensed water well drillers in your area. A professional driller will handle the job safely and correctly, giving you peace of mind and a reliable source of water for years to come.